Simplify your products!
DESIGN TO COST
Design to Cost is a structured approach that allows to achieve a very competitive cost price by taking action at the product and service design stage.
It aims to bring costs within a defined target by using all the savings levers, even by adjusting functionalities and performance if necessary.
It seeks to satisfy the right needs at the best cost and is characterised by its very direct and pragmatic approach.
Design to Cost is effective if it brings together the relevant skills in a constructive team effort, condensed in time and sufficiently thorough to question established habits and patterns.
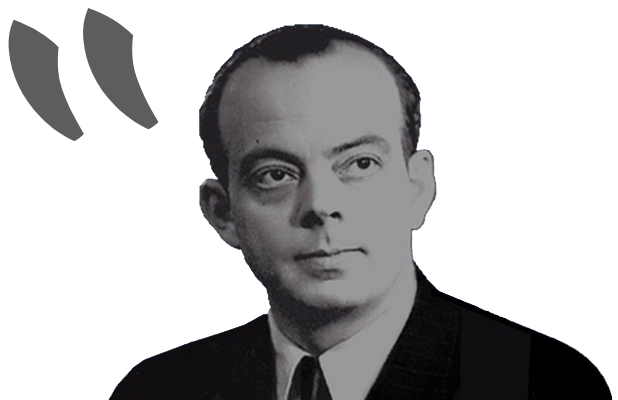
Competitiveness potentials largely underestimated
All products and systems hide unsuspected saving potentials, which surprise the teams themselves when they come to light.
Yves Dubreil’s(*) famous drawing has popularised the competitive opportunities that a Design to Cost almost always reveals:
- The weight of habits let whole sections of the cost chain being repeated without question,
- “Beautiful technique” sometimes leads designers, keen on excellence and performance, towards too much sophistication and complexity,
- Safety margins push to over-design and over-quality.
To this triptych should be added the ‘letter to Santa’ specifications, which demand ever higher performance, even where the customer will not pay much attention.
Not to mention the bad choices of standardisation which, in order to reduce the diversity of products and components, generate “envelope” costs on complete ranges.
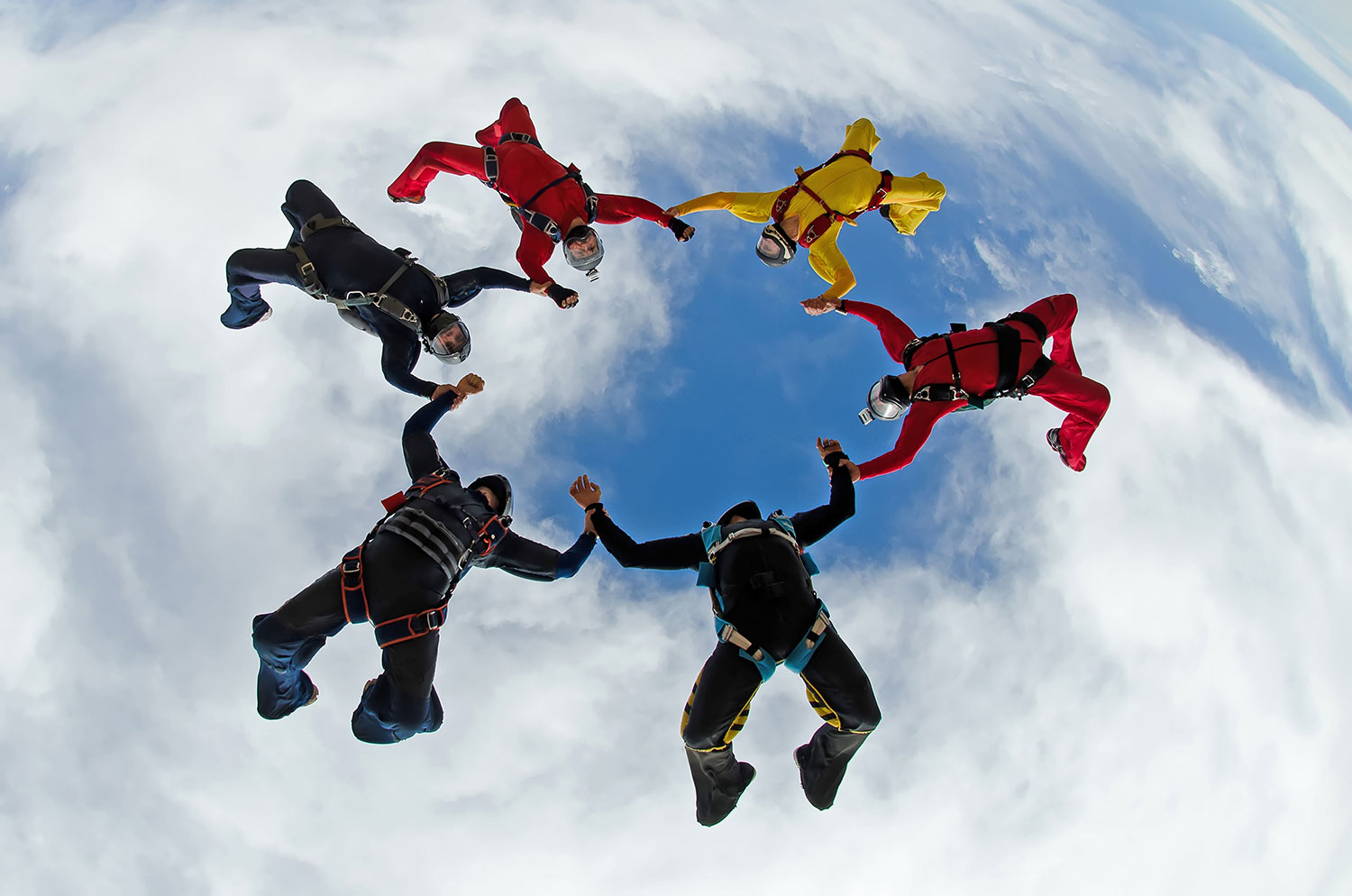
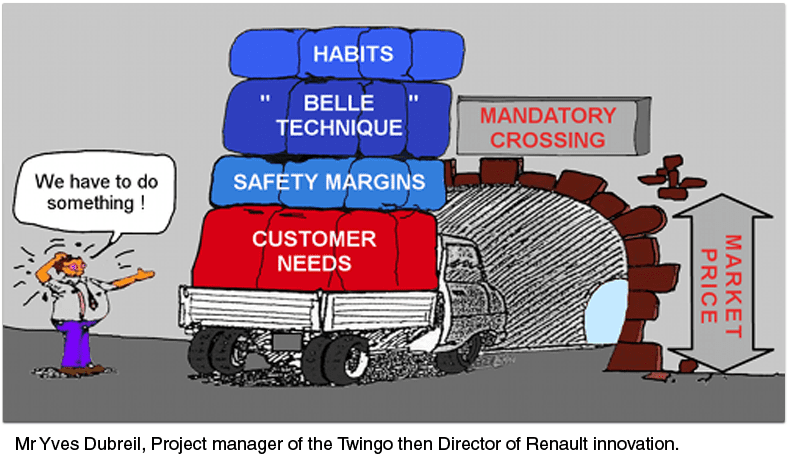
Too much sequential operation, in silos
Many parts of the company feel responsible for reducing and controlling costs: buyers and supply chain, designers, industrialisation teams, management control, etc.
However, they rarely manage to work well as a team and avoid misunderstandings and multiple iterations.
The costs, discovered too late and far from the initial objectives, then trigger the panic mode!
However, it is the simultaneity of thinking and the early sharing of the impacts of choices (of specification, structure, technology, industrialisation, etc.) that conditions the convergence towards the most attractive and competitive offer.
Simplifying products from the inside…
The essence of Design to Cost is to focus costs on true customer value.
It is therefore important to look at the perceived value and the right needs, but also to look for simplification potentials along the cost chain very quickly.
And aim to eliminate everything that is not essential for the satisfaction of real needs.
… with a simple approach!
To lead teams to the best choices by the shortest route, it is necessary to adopt an approach that goes to the heart of the matter!
The effectiveness of Design to Cost is based on simple and quick tools – and above all not hyper-analytical – that detect the priority levers:
Functional Analysis:
Quick and synthetic, it must question the customer value and the right needs by focusing on the key requirements.
It is a question of distinguishing between imperative needs and “nice to have”, which will be arbitrated according to their obtaining costs and feasibility.
Benchmarking :
Conducted in a “flash” way, it scans the choices of the major competitors and highlights the significant differences in response to needs and solutions.
Value Analysis:
It goes through the whole chain to distinguish “Just Necessary” costs from potentials of questionable cost.
It thus offers, early in the project, a complete mapping of competitiveness levers (Specification, Architecture, Simplification, Process, Sourcing, etc.).
Creativity:
It explores all facets of the offer and imagines possible solutions to address real needs and eradicate unnecessary costs.
Concept Evaluation:
It characterises the possible concepts and solutions in order to converge consensually towards the best compromises.
Structured and reproducible, the Design to Cost approach plays an eminently pedagogical role and, thanks to its highly demonstrative results, encourages a new way of team working.
Conditions for success
Ambitious targets are the key to successful design to cost:
They are equal to the challenge and show the need to go beyond the usual habits and results.
Clearly expressed by the Management, they contribute to the mobilisation of energies.
The multidisciplinary approach must of course involve the whole project team – right down to the key partners and suppliers – in a collegial and constructive work.
Une des forces de la méthodologie est de ne pas statuer trop tôt sur l’acceptabilité ou la faisabilité des solutions : les arbitrages ne se feront qu’avec la pleine visibilité des enjeux (besoins, coûts, risques) pour l’équipe projet et la Direction.
A dynamic and positive animation:
Leading a Design to Cost is not a matter for specialists in a particular field and a broad, multi-sectoral expertise is an asset.
The most important thing is a simple methodology and good management of the human factor:
The aim is to create a dynamic and to lead the team, through constructive exchanges, towards the right levels of questioning, with pleasure and enthusiasm.
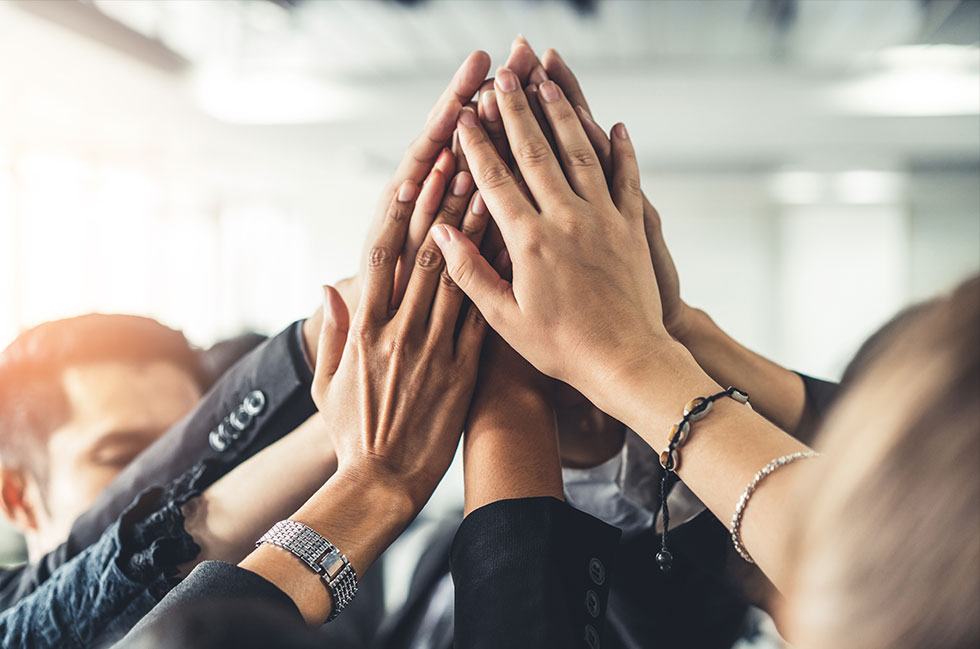
Extremely varied applications
Essential approach, Design to Cost is now implemented in all sectors of activity :
- Large, medium and small series products,
- Services,
- Industrial machinery and equipment,
- Complete plants and installations, single or reproducible,
- Responses to calls for tenders,
- B2B and B2C…
It is the subject of numerous naming variations:
- Design to Cost, for new projects,
- Redesign to Cost, for existing systems,
- Design to weight, aiming to reduce masses
- Design to Manufacturing, seeking the best industrialisation and manufacturability…
- And of course, Design to Value, with a focus on Innovation and Customer Value…
But for us, Design to Cost and Value remains the ideal synthesis, the global approach that does not neglect any of the aspects of the attractiveness and competitiveness of the future offer!
Radical gains
The benefits of Design to Cost are high and often surprising:
- Radical reduction of direct costs: -15, -30 or even -50% on new or existing products
- Reduced development and investment costs
- Reduction of CAPEX and OPEX costs of industrial installations
- Savings on Life cycle cost and Total Cost of Ownership
The gains also go beyond economic benefits alone:
- Reduction of development time, thanks to efficient exchanges and less iterations
- And above all, the impetus for change, thanks to a collegial approach and strengthened team cohesion.
YOU HAVE A PROJECT?
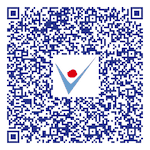